Undercuts in Plastic, 1 of 3.
Wait a minute. You want me to add an undercut?
ENGINEERING AND DESIGN STUFFPLASTIC PART DESIGN
Bert
10/12/20231 min read
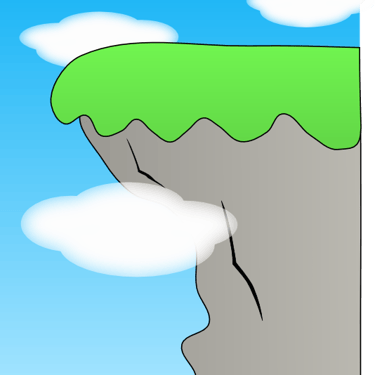
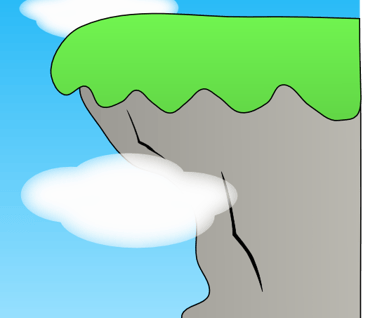
In sales, it may be good to undercut your competition but for plastic part design, you don’t undercut your part. When you learn to design parts for plastic injection molding, the first two rules that you learn are maintain a uniform wall thickness and avoid undercuts. (Maybe you were expecting "make adequate draft"? For the most part, draft is required due to texture and surface imperfections, aka very small undercuts.) In fact, probably all other rules are variations of those two or the best way to break the rules if you have to. So, imagine my surprise years ago the first time a mold maker told me I needed to add undercuts to my part design. Huh?
One rule for molders and mold-makers is to make sure your part stays on the core. (Which side is the core you ask? See this post.) In some parts, there is a lot of detail on the cavity side and maybe not as much draft as you would like to have. If at the same time there are few features and lots of draft on the core side, that is a good recipe for the part sticking to the cavity. Why is that a problem? The ejection is on the core (most of the time) and if the part doesn’t fall off the mold or isn’t there for the robot to retrieve it, you have a problem. That problem can lead to damaged molds. Therefore, you got to keep that part on the core so it can be properly ejected. The simplest way to do that is to add some undercuts to the core side details. A depth of about .010” and a length of .200” should do the trick but check with your molder and mold-maker for what works best for your design.