Snap Fit Paradox
Some advice on snap fit design in plastic parts.
PLASTIC PART DESIGNENGINEERING AND DESIGN STUFF
8/31/20231 min read
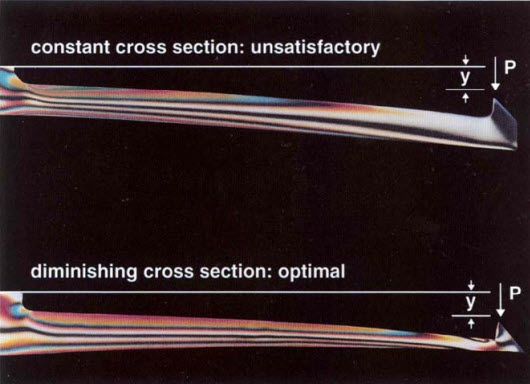
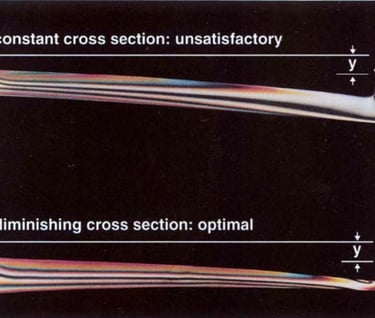
Technically, it is not a paradox but the situation is a little counterintuitive. Here is the problem. You have designed a snap fit arm and when you assemble the parts, the snap arm breaks. Your initial reaction is that when something breaks, it isn’t strong enough and you need to make it stronger. In this case, that is most likely the wrong thing to do.
It is this situation that I call the snap fit paradox. What is probably the problem is that the snap arm is too strong not too weak. An important aspect of this problem is that it is breaking on assembly, not during use. Therefore, the stress on the arm is determined by how much the arm deflects, which is governed by the engagement or overlap between the snap arm hook and the edge it engages. Making the snap arm stronger by increasing stiffness in this case of fixed strain, or more properly, fixed displacement, causes even more stress and it will still break. To reduce the stress, you need to make it weaker and/or distribute the stress. Making it thinner is one way to make it weaker. Tapering the cross section of the arm distributes the stress and makes it a little weaker, which is best practice for most snap arms. The hazard is this can turn into a tail chasing exercise if the weaker arm is no longer strong enough to keep the parts together. Solving that is a post for another day.
Snap fits are tricky things to get right. Whole books and lots of design guides have been written about them. Here is link to snap fit guide that I have used. For a book on the subject, try The First Snap-Fit Handbook by Paul Bonenberger. Not a light read and it is such a thorough and compressive approach to snap-fit design that the first time I looked at it, it was not useful to me. Let's call it operator error. After attending his course in 2002, it made a lot more sense. I recommend it.